PackingSim/i-Caps
最適積み付けシステム
PackingSim/i-Caps 事例
コンテナ荷積み 積み付け調整の容易化と空きスペースを最小とする積載計画を算出
お客様の抱える問題点とOR部による解決
積載計画作成に時間がかかる → 5分で積載計画作成を可能に
もともと、航空貨物特有のコンテナ形状に合わせた積載計画が必要で、自動化が困難な分野です。 さらに、近年は航空貨物事業の変化(小口の顧客の増加、パレットの増加*)に伴って計画作成はより複雑化。 計画作成時間は増大し、それによって起こる機会損失や信用低下も懸念されていました。
弊社の開発した新しい航空貨物積載シミュレーションシステムは、それまで30分かかっていた積載作成を 5分で完了。他社よりも早く見積もりを出せるようになりました。
また、過去に似たような計画を作成した結果が保存されていれば、そこから手を加えることもできる システムを組みました。
*…積み付けは現場で行うが、パレットの場合だとどの位の高さまで積めばいいのか、 現場で判断ができないため、コンテナの積み付けよりも勘に頼るところが多く難しい。
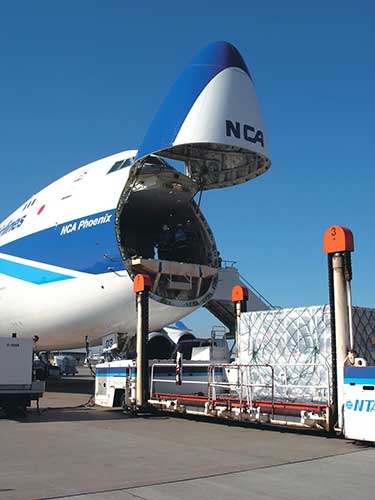
積載計画を作成できる人間が限られる → 半年~1年かかる積載計画作成担当者教育を1か月に短縮
新システムでは、Webブラウザ上で、誰でも扱えるインターフェースを開発。 積みつけに必要な条件は全てシステムに組み込まれているため、作業は、計算に必要な項目の入力のみとなり、 それまで半年~1年かかっていた積載計画担当者の教育期間を1カ月に短縮。 担当者が増えたことで複数拠点での作業ができ、また積み付け担当者によるばらつきもなくなり、 迅速で高精度の見積もり回答を実現しました。
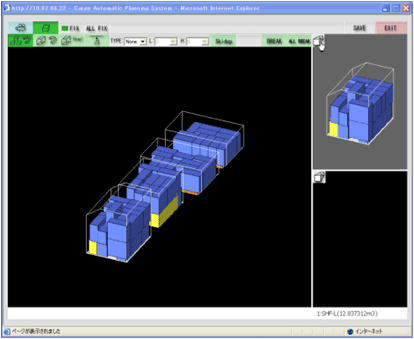
積載計画に修正が必要 → 積み付け結果の3D表示
これまで使っていたシステムでは、多くの場合修正が必要で、 誤った積載計画があると現場が混乱することもありました。
そこで、積み付け結果を正確かつ簡単に評価できるように、3Dで表示。 さらに、積み付け担当者への搭載指示書の出力機能も搭載。詳細な積載位置が表記されるため、 ミスを減らし、スムーズな搭載を可能にしました。
積載効率が悪い → お客様の考える理想の積み付けをヒアリングし、システム化
無駄な輸送が多ければコストは増加します。また、環境問題への配慮として、 CO2の削減にも取り組みたいとの要望もありました。
そこで、積み付け時に考慮している様々な指標をもとに、積み付けアルゴリズムを検討し、 システムに組み込みました。
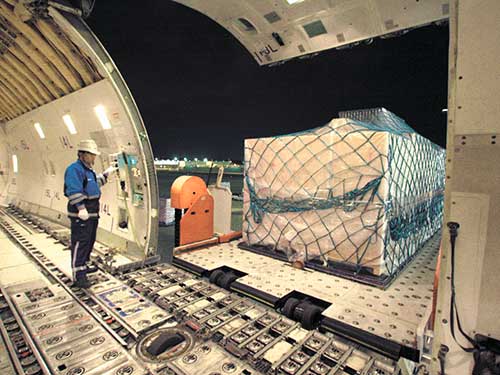
解決までの手順
ヒアリング。理想とする積み付けプランとは?
まず、理想とする積み付けプランがどんなものであるかについて、調査・ヒアリングを行いました。
そこで、以下のような「最適な積み付け」が理想とされていることが分かりました。
- 積載体積が大きい
- 使用コンテナ数が少ない
- 重心が低い
最適積み付けエンジンの開発
次に、実際にこれらの指標をもとに積み付けアルゴリズムの検討に入りました。
一般的な積み付け問題では厳密な最良解を求めようとすると、膨大な計算時間がかかってしまいます。
今回は実際の業務で使われることを考慮して、解の精度(良さ)と計算時間のバランスを調整することのできる ヒューリスティックアルゴリズム(*)を独自に考案し、エンジンに組み込みました。
プロジェクトではエンジンの試作が終わった段階で、そこで得られた解が業務で受け入れられるかどうか (人間が見て違和感がないかどうか)を担当者の方に一度見ていただきました。
その上で、チューニングをした物を最終的に採用しました。
今回開発したアルゴリズムとその成果は多くの学会で発表され(OR学会大会、RAMP等)アルゴリズムは 特許申請済です。
*…試行錯誤的に解を求めていく手法。 ある程度の精度の解を比較的短時間で得られることが特徴。
作業効率を上げるユーザーインターフェイスの開発
案件登録から計算、3Dによる積み付け結果の確認・修正、帳票出力をWebプラウザ上で行うための 仕組みづくりも同時に開発しました。
学会発表
斉藤努、矢野夏子「離散最適化の事例:航空貨物コンテナの最適詰め込みと大都市災害における 緊急物資の最適配送計画」、日本オペレーションズ・リサーチ学会RAMP2007, 2007年10月